Đĩa mài đóng vai trò quan trọng trong nhiều ngành công nghiệp, tạo điều kiện thuận lợi cho việc định hình và hoàn thiện vật liệu. Tuy nhiên, giống như bất kỳ công cụ nào khác, chúng không tránh khỏi các vấn đề có thể cản trở hiệu quả và hiệu suất của chúng. Trong bài viết này, chúng tôi sẽ đi sâu vào các vấn đề phổ biến của đĩa mài, khám phá nguyên nhân gốc rễ của chúng và cung cấp các giải pháp hiệu quả cho quy trình làm việc liền mạch.
Giới thiệu
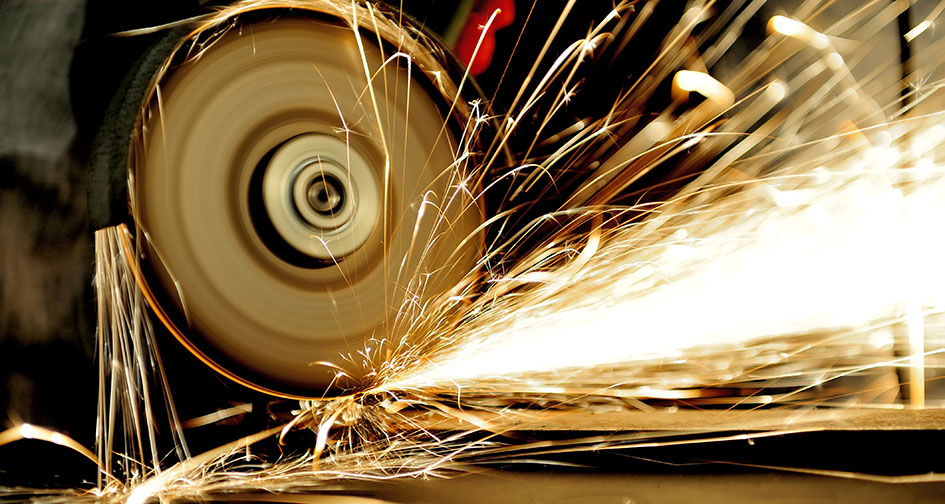
Đĩa mài đóng vai trò cơ bản trong nhiều ngành công nghiệp, đóng vai trò là công cụ thiết yếu cho quá trình loại bỏ vật liệu, định hình và hoàn thiện. Hiểu được định nghĩa, tầm quan trọng của chúng trong các ngành công nghiệp và các vấn đề chung gặp phải là rất quan trọng để tối ưu hóa việc sử dụng chúng và đảm bảo hoạt động hiệu quả.
A. Định nghĩa về đĩa mài
Đĩa mài là dụng cụ mài mòn được sử dụng trong các quy trình gia công để cắt, mài hoặc đánh bóng bề mặt vật liệu. Các đĩa này thường bao gồm các hạt mài mòn được liên kết với vật liệu nền, tạo ra một dụng cụ quay có thể loại bỏ vật liệu thừa, làm mịn bề mặt hoặc làm sắc cạnh. Chúng có nhiều hình dạng và kích thước khác nhau, mỗi loại được thiết kế cho các ứng dụng cụ thể.
B. Tầm quan trọng trong nhiều ngành công nghiệp khác nhau
Ngành gia công kim loại:
Trong chế tạo và sản xuất kim loại, đĩa mài rất quan trọng để định hình, loại bỏ gờ và hoàn thiện bề mặt kim loại. Chúng thường được sử dụng với máy mài góc để đạt được kích thước chính xác và chất lượng bề mặt.
Ngành xây dựng:
Các chuyên gia xây dựng sử dụng đĩa mài cho các nhiệm vụ như chuẩn bị bề mặt bê tông, làm mịn các cạnh thô và loại bỏ các khuyết điểm trên vật liệu như đá và bê tông.
Ngành công nghiệp ô tô:
Đĩa mài là thiết yếu trong ngành ô tô cho các nhiệm vụ từ mài dụng cụ đến định hình và hoàn thiện các thành phần kim loại. Chúng góp phần vào độ chính xác và chất lượng của các bộ phận ô tô.
Ngành chế biến gỗ:
Thợ mộc sử dụng đĩa mài để định hình và làm mịn bề mặt gỗ. Những đĩa này có hiệu quả trong việc loại bỏ vật liệu thừa, tinh chỉnh hình dạng và chuẩn bị gỗ để hoàn thiện thêm.
Sản xuất chung:
Đĩa mài được ứng dụng trong nhiều quy trình sản xuất khác nhau, nơi cần loại bỏ vật liệu chính xác, góp phần sản xuất ra các linh kiện chất lượng cao.
C. Các vấn đề thường gặp
Sự mài mòn và hao mòn của đĩa:
Việc sử dụng liên tục có thể dẫn đến mòn và mài mòn đĩa mài, ảnh hưởng đến hiệu suất của nó. Cần kiểm tra và thay thế thường xuyên để duy trì hiệu quả.
Quá nhiệt:
Ma sát quá mức trong quá trình sử dụng kéo dài có thể dẫn đến quá nhiệt, ảnh hưởng đến độ bền của đĩa và chất lượng bề mặt hoàn thiện. Các biện pháp làm mát thích hợp và nghỉ ngơi định kỳ là điều cần thiết.
Tắc nghẽn:
Đĩa mài có thể tích tụ cặn vật liệu, làm giảm hiệu quả của chúng. Việc vệ sinh thường xuyên hoặc chọn đĩa có tính năng chống tắc nghẽn giúp ngăn ngừa vấn đề này.
Rung động và lắc lư:
Sự mất cân bằng hoặc hao mòn không đều có thể dẫn đến rung động hoặc lắc lư, ảnh hưởng đến cả chất lượng hoàn thiện và sự an toàn của hoạt động. Việc lắp đặt và cân bằng đúng cách là rất quan trọng.
Chọn đĩa không đúng:
Việc lựa chọn sai loại đĩa mài cho một vật liệu hoặc ứng dụng cụ thể có thể dẫn đến kém hiệu quả và hư hỏng tiềm ẩn. Việc lựa chọn đúng dựa trên khả năng tương thích của vật liệu là điều cần thiết.
Hiểu được định nghĩa, ý nghĩa và những thách thức tiềm ẩn liên quan đến đĩa mài là điều cần thiết đối với các ngành công nghiệp dựa vào các công cụ này. Bằng cách giải quyết các vấn đề chung và đảm bảo sử dụng đúng cách, các ngành công nghiệp có thể tối đa hóa hiệu quả của đĩa mài trong các ứng dụng tương ứng của họ.
Sự hao mòn của đĩa mài
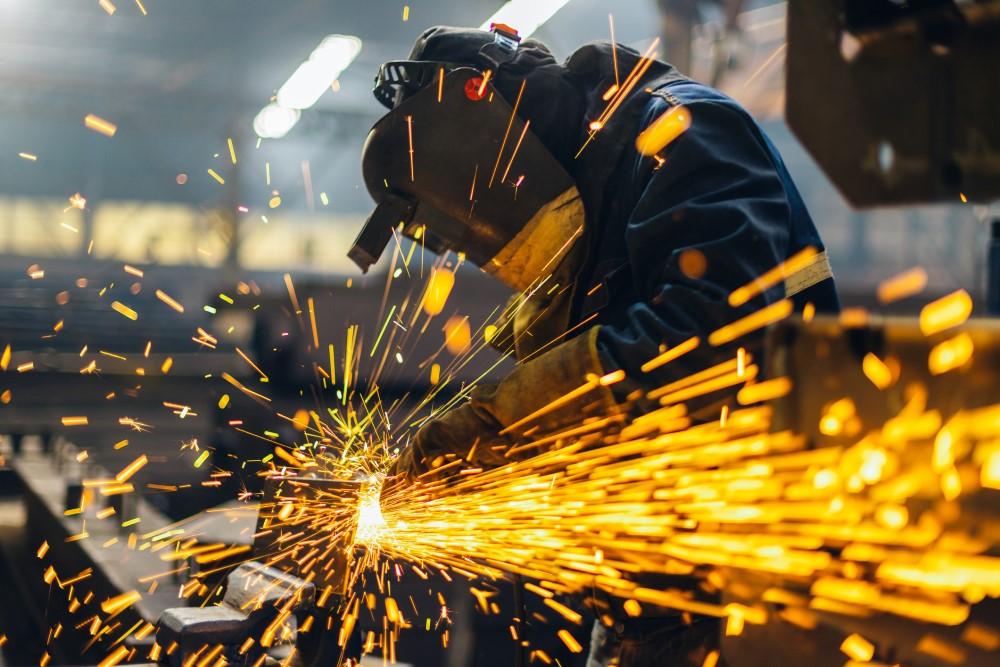
Đĩa mài là công cụ thiết yếu trong nhiều ngành công nghiệp, cung cấp độ mài mòn cần thiết cho các nhiệm vụ từ chế tạo kim loại đến đánh bóng bê tông. Hiểu được các yếu tố góp phần gây hao mòn trên đĩa mài là rất quan trọng để tối ưu hóa hiệu suất của chúng và đảm bảo an toàn.
Độ cứng và thành phần vật liệu:
Độ cứng thay đổi:Đĩa mài tiếp xúc với các vật liệu có độ cứng khác nhau. Các vật liệu mài mòn như kim loại và bê tông có thể có độ cứng khác nhau đáng kể. Việc mài liên tục trên các vật liệu cứng sẽ làm tăng tốc độ mài mòn.
Thành phần vật liệu:Sự hiện diện của các thành phần mài mòn trong vật liệu được mài có thể ảnh hưởng đến độ mài mòn của đĩa mài. Các hạt mài mòn có thể đẩy nhanh quá trình mài mòn của đĩa.
Áp suất và lực nghiền:
Áp suất quá mức:Việc tác dụng lực quá mức lên đĩa mài có thể khiến đĩa bị mòn nhanh hơn. Điều cần thiết là phải sử dụng lực được khuyến nghị cho ứng dụng cụ thể để tránh gây áp lực không cần thiết lên đĩa.
Lực lượng không đủ: Mặt khác, lực không đủ có thể dẫn đến việc mài kéo dài, tạo thêm ma sát và nhiệt, góp phần gây mài mòn.
Chất lượng và thành phần của đĩa:
Chất lượng vật liệu mài mòn:Chất lượng của vật liệu mài mòn được sử dụng trong đĩa mài ảnh hưởng đáng kể đến tuổi thọ của nó. Vật liệu mài mòn chất lượng cao có xu hướng chống mài mòn và duy trì độ sắc nét lâu hơn.
Chất kết dính:Chất kết dính giữ các hạt mài mòn lại với nhau đóng vai trò quan trọng. Chất kết dính được thiết kế tốt sẽ tăng cường độ bền của đĩa.
Điều kiện môi trường làm việc:
Nhiệt độ:Nhiệt độ cao sinh ra trong quá trình mài có thể ảnh hưởng đến thành phần của đĩa. Nhiệt độ quá cao làm yếu chất kết dính và tăng tốc độ mài mòn.
Độ ẩm và chất gây ô nhiễm:Việc tiếp xúc với độ ẩm hoặc chất gây ô nhiễm trong môi trường làm việc có thể ảnh hưởng đến tính toàn vẹn của đĩa mài, dẫn đến mòn nhanh hơn.
Kỹ thuật vận hành:
Kỹ thuật đúng:Kỹ năng và kỹ thuật của người vận hành là rất quan trọng. Sử dụng không đúng cách, chẳng hạn như mài ở góc không chính xác hoặc sử dụng lực quá mức, có thể góp phần gây ra tình trạng mòn không đều và làm giảm tuổi thọ của đĩa.
Kiểm tra thường xuyên:Người vận hành nên thường xuyên kiểm tra đĩa mài để xem có dấu hiệu hư hỏng hoặc mòn nào không. Đĩa mài mòn vượt quá một điểm nhất định cần được thay thế ngay.
Khả năng tương thích của kích thước đĩa và vòng tua máy:
Kích thước chính xác:Sử dụng đúng kích thước đĩa cho máy mài là rất quan trọng. Đĩa có kích thước không phù hợp có thể mòn không đều hoặc gây ra rủi ro về an toàn.
Khả năng tương thích RPM:Việc tuân thủ số vòng quay mỗi phút (RPM) được khuyến nghị cho đĩa mài sẽ đảm bảo hiệu suất tối ưu và ngăn ngừa mài mòn sớm.
Bảo dưỡng thường xuyên, tuân thủ các điều kiện vận hành được khuyến nghị và lựa chọn đĩa mài phù hợp cho nhiệm vụ là những biện pháp thiết yếu để giảm thiểu hao mòn. Bằng cách hiểu các yếu tố ảnh hưởng đến hao mòn, người vận hành có thể nâng cao tuổi thọ và hiệu quả của đĩa mài, góp phần vào hoạt động mài an toàn và năng suất hơn.
Mài không đều
Mài không đều là tình huống mà bề mặt được mài không đạt được độ hoàn thiện đồng đều và mịn. Vấn đề này có thể phát sinh vì nhiều lý do khác nhau và có thể ảnh hưởng đến chất lượng của phôi. Sau đây là các yếu tố phổ biến góp phần vào quá trình mài không đều và các giải pháp tiềm năng:
Lựa chọn đá mài không đúng:
Giải pháp:Đảm bảo rằng bánh mài phù hợp với vật liệu được mài. Các vật liệu khác nhau yêu cầu các đặc tính mài mòn cụ thể. Chọn loại bánh mài, kích thước hạt và độ liên kết phù hợp cho ứng dụng.
Việc điều chỉnh bánh xe không đúng cách:
Gây ra:Đá mài không được mài đúng cách có thể dẫn đến mài mòn không đều và cắt không hiệu quả.
Giải pháp:Thường xuyên mài nhẵn bánh mài để duy trì hình dạng và loại bỏ mọi mảnh vụn tích tụ. Việc mài nhẵn đúng cách đảm bảo bề mặt cắt đồng nhất.
Chất lỏng nghiền hoặc chất làm mát không đủ:
Gây ra:Việc sử dụng chất lỏng mài không đủ hoặc không đúng cách có thể làm tăng ma sát và nhiệt, dẫn đến mài không đều.
Giải pháp:Sử dụng chất lỏng mài hoặc chất làm mát thích hợp để tản nhiệt và giảm ma sát. Làm mát đúng cách là điều cần thiết để đạt được kết quả đồng đều.
Thông số nghiền không chính xác:
Gây ra:Sử dụng các thông số mài không chính xác như tốc độ, tốc độ nạp liệu hoặc độ sâu cắt quá mức có thể dẫn đến mài không đều.
Giải pháp:Điều chỉnh các thông số nghiền theo yêu cầu của vật liệu và ứng dụng. Tham khảo khuyến nghị của nhà sản xuất để biết cài đặt tối ưu.
Bánh mài mòn:
Gây ra:Bánh mài mòn có thể không cung cấp được bề mặt cắt đồng nhất, dẫn đến việc mài không đều.
Giải pháp:Thay thế bánh mài khi nó đã hết tuổi thọ sử dụng. Kiểm tra bánh mài thường xuyên để xem có dấu hiệu mòn không.
Áp suất hoặc tốc độ cấp liệu không đều:
Gây ra:Áp suất không đều hoặc tốc độ nạp liệu không đồng đều trong quá trình nghiền có thể dẫn đến việc loại bỏ vật liệu không đều.
Giải pháp:Áp dụng lực ép đồng đều và duy trì tốc độ cấp liệu nhất quán trên toàn bộ phôi. Kỹ năng của người vận hành và sự chú ý đến từng chi tiết là rất quan trọng.
Sự cố máy móc:
Gây ra:Các vấn đề cơ học với máy mài, chẳng hạn như sai lệch hoặc trục chính có vấn đề, có thể dẫn đến việc mài không đều.
Giải pháp:Tiến hành kiểm tra bảo dưỡng thường xuyên cho máy mài. Xử lý kịp thời mọi vấn đề về cơ học để đảm bảo máy hoạt động bình thường.
Cố định phôi:
Gây ra:Các phôi gia công không được cố định chắc chắn hoặc không thẳng hàng có thể dẫn đến quá trình mài không đều.
Giải pháp:Đảm bảo cố định và căn chỉnh phôi đúng cách. Cố định chặt để tránh chuyển động trong quá trình mài.
Để giải quyết tình trạng mài không đều, cần kết hợp giữa thiết lập thiết bị phù hợp, thông số vận hành chính xác và các biện pháp bảo dưỡng thường xuyên. Người vận hành cần được đào tạo để xác định và khắc phục sự cố kịp thời nhằm đạt được kết quả chất lượng cao và nhất quán trong các ứng dụng mài. Kiểm tra thường xuyên và tuân thủ các biện pháp tốt nhất góp phần loại bỏ vật liệu hiệu quả và đồng đều trong quá trình mài.
Vấn đề quá nhiệt
Quá nhiệt trong quá trình mài là một vấn đề phổ biến có thể ảnh hưởng đến hiệu suất của cả bánh mài và phôi. Nhiệt độ quá cao có thể dẫn đến nhiều vấn đề khác nhau, bao gồm giảm tuổi thọ của bánh mài, hư hỏng do nhiệt đối với phôi và giảm hiệu quả mài nói chung. Sau đây là các nguyên nhân tiềm ẩn và giải pháp để giải quyết các vấn đề quá nhiệt:
Thông số nghiền không chính xác:
Gây ra:Sử dụng các thông số mài không phù hợp, chẳng hạn như tốc độ, tốc độ nạp liệu hoặc độ sâu cắt quá mức có thể tạo ra nhiệt dư thừa.
Giải pháp:Điều chỉnh các thông số nghiền trong phạm vi khuyến nghị. Tham khảo hướng dẫn của nhà sản xuất để biết cài đặt tối ưu dựa trên vật liệu được nghiền.
Làm mát hoặc bôi trơn không đủ:
Gây ra:Việc sử dụng không đủ chất làm mát hoặc chất lỏng mài có thể làm tăng ma sát và nhiệt.
Giải pháp:Đảm bảo cung cấp đủ chất làm mát hoặc chất bôi trơn trong quá trình mài. Làm mát đúng cách giúp tản nhiệt và ngăn ngừa hư hỏng do nhiệt.
Chọn bánh xe không đúng:
Gây ra:Việc lựa chọn đá mài có thông số kỹ thuật không phù hợp với vật liệu cần mài có thể dẫn đến hiện tượng quá nhiệt.
Giải pháp:Chọn bánh mài có loại mài mòn, kích thước hạt và độ liên kết phù hợp với ứng dụng cụ thể. Việc kết hợp bánh mài với vật liệu sẽ giảm thiểu sự tỏa nhiệt.
Các vấn đề về vật liệu phôi:
Gây ra:Một số vật liệu, đặc biệt là những vật liệu có độ dẫn nhiệt kém, dễ bị quá nhiệt trong quá trình nghiền.
Giải pháp:Điều chỉnh thông số nghiền cho các vật liệu có độ dẫn nhiệt thấp hơn. Cân nhắc sử dụng bánh mài chuyên dụng được thiết kế cho các vật liệu nhạy nhiệt.
Các vấn đề về chỉnh bánh xe:
Gây ra:Sự không đồng đều hoặc lắp đặt không đúng cách của đá mài có thể dẫn đến tiếp xúc không đều và tích tụ nhiệt.
Giải pháp:Thường xuyên mài bánh mài để duy trì hình dạng và loại bỏ bất kỳ lớp phủ hoặc mảnh vụn tích tụ nào. Bánh mài được mài đúng cách đảm bảo hiệu suất mài đồng đều.
Bảo trì máy không đầy đủ:
Gây ra:Máy mài được bảo dưỡng kém có thể gây ra vấn đề quá nhiệt.
Giải pháp:Tiến hành bảo dưỡng máy mài thường xuyên, bao gồm kiểm tra hệ thống làm mát, kiểm tra thiết bị mài bánh xe và đảm bảo căn chỉnh đúng cách. Xử lý kịp thời mọi vấn đề về cơ học.
Lưu lượng chất làm mát bánh xe không đủ:
Gây ra:Lưu lượng chất làm mát không đủ đến vùng nghiền có thể làm giảm khả năng tản nhiệt.
Giải pháp:Kiểm tra và tối ưu hóa hệ thống cung cấp chất làm mát. Đảm bảo chất làm mát tiếp cận hiệu quả vùng nghiền để duy trì hiệu quả làm mát.
Thời gian nghiền quá mức:
Gây ra:Việc nghiến răng kéo dài mà không nghỉ ngơi có thể dẫn đến tích tụ nhiệt.
Giải pháp:Thực hiện mài ngắt quãng và cho phép nghỉ để tránh tích tụ nhiệt quá mức. Cách tiếp cận này đặc biệt quan trọng đối với các nhiệm vụ mài lớn hoặc khó khăn.
Giải quyết các vấn đề quá nhiệt trong quá trình mài đòi hỏi một cách tiếp cận toàn diện bao gồm thiết lập thiết bị phù hợp, các thông số mài phù hợp và các biện pháp bảo trì thường xuyên. Người vận hành nên theo dõi và kiểm soát quá trình sinh nhiệt trong quá trình mài để đảm bảo hiệu suất tối ưu, kéo dài tuổi thọ dụng cụ và kết quả chất lượng cao.
Mối quan tâm về rung động
Rung động quá mức trong quá trình mài có thể dẫn đến nhiều vấn đề khác nhau, bao gồm chất lượng bề mặt giảm, tăng độ mòn dụng cụ và khả năng gây hư hỏng cho máy mài. Việc giải quyết các vấn đề về rung động là rất quan trọng để đạt được các quy trình mài chính xác và hiệu quả. Sau đây là các nguyên nhân tiềm ẩn và giải pháp để giảm thiểu các vấn đề rung động:
Bánh xe mòn không đều:
Gây ra:Sự mài mòn không đều trên đá mài có thể dẫn đến tiếp xúc không đều với phôi, gây ra rung động.
Giải pháp:Kiểm tra và bảo dưỡng bánh mài thường xuyên để duy trì bề mặt đồng đều và phẳng. Bảo dưỡng bánh mài đúng cách giúp giảm thiểu độ rung.
Đá mài không cân bằng:
Gây ra:Sự mất cân bằng ở đá mài, do mòn không đều hoặc do lỗi sản xuất, đều có thể dẫn đến rung động.
Giải pháp:Cân bằng bánh mài bằng máy cân bằng bánh mài. Cân bằng đảm bảo phân bổ trọng lượng đều và giảm độ rung trong quá trình vận hành.
Hiệu chuẩn máy không đầy đủ:
Gây ra:Việc hiệu chuẩn kém hoặc căn chỉnh không đúng các bộ phận của máy, chẳng hạn như trục chính bánh xe hoặc bàn làm việc, có thể gây ra rung động.
Giải pháp:Hiệu chuẩn và căn chỉnh các bộ phận máy thường xuyên để đảm bảo chức năng hoạt động bình thường. Thực hiện theo hướng dẫn của nhà sản xuất về thiết lập và căn chỉnh máy.
Sự mất cân bằng của phôi:
Gây ra:Một phôi gia công không bằng phẳng hoặc không được cố định đúng cách có thể gây mất cân bằng và gây ra rung động.
Giải pháp:Cố định phôi đúng cách, đảm bảo phôi được định vị và kẹp đều. Xử lý mọi vấn đề mất cân bằng trước khi bắt đầu quá trình mài.
Chọn bánh xe không đúng:
Gây ra:Sử dụng đá mài có thông số kỹ thuật không phù hợp có thể gây ra rung động.
Giải pháp:Chọn bánh mài có loại mài mòn, kích thước hạt và độ liên kết phù hợp với vật liệu cần mài. Việc chọn bánh mài phù hợp với ứng dụng sẽ giảm thiểu độ rung.
Hao mòn máy móc:
Gây ra:Các bộ phận máy bị mòn hoặc hư hỏng, chẳng hạn như ổ trục hoặc trục chính, có thể gây ra rung động.
Giải pháp:Kiểm tra và thay thế các bộ phận máy bị mòn thường xuyên. Bảo dưỡng đúng cách giúp ngăn ngừa rung động quá mức và kéo dài tuổi thọ của máy mài.
Lưu lượng chất làm mát không đủ:
Gây ra:Lượng chất làm mát không đủ chảy đến vùng nghiền có thể dẫn đến tích tụ nhiệt và rung động.
Giải pháp:Tối ưu hóa hệ thống cung cấp chất làm mát để đảm bảo làm mát đúng cách. Làm mát hiệu quả làm giảm nguy cơ giãn nở và co lại do nhiệt, có thể dẫn đến rung động.
Các vấn đề về giá đỡ dụng cụ:
Gây ra:Các vấn đề với giá đỡ dụng cụ hoặc giao diện trục chính có thể gây ra rung động.
Giải pháp:Đảm bảo giá đỡ dụng cụ được lắp chắc chắn và căn chỉnh đúng với trục chính. Sử dụng giá đỡ dụng cụ chất lượng cao và được bảo dưỡng đúng cách để giảm thiểu rung động.
Nền tảng máy móc:
Gây ra:Nền tảng máy kém hoặc hỗ trợ không đầy đủ có thể làm tăng độ rung.
Giải pháp:Đảm bảo máy mài được lắp đặt trên nền móng ổn định và được thiết kế đúng cách. Xử lý mọi vấn đề về kết cấu để giảm thiểu rung động truyền đến máy.
Giải quyết hiệu quả các vấn đề về rung động trong quá trình mài đòi hỏi sự kết hợp giữa bảo dưỡng máy, lựa chọn bánh xe và xử lý phôi gia công phù hợp. Người vận hành nên thực hiện các biện pháp kiểm tra và bảo dưỡng thường xuyên để xác định và giải quyết các vấn đề kịp thời, giúp cải thiện hiệu suất và chất lượng mài.
Các vấn đề tải trong quá trình nghiền
Tải trong quá trình mài là hiện tượng các khoảng trống giữa các hạt mài trên bánh mài được lấp đầy bằng vật liệu đang được mài, dẫn đến giảm hoạt động cắt và tăng ma sát. Tải có thể ảnh hưởng tiêu cực đến hiệu quả và chất lượng của quá trình mài. Sau đây là các nguyên nhân tiềm ẩn và giải pháp để giải quyết các vấn đề về tải:
Vật liệu phôi mềm:
Gây ra:Việc nghiền các vật liệu mềm có thể khiến các hạt mài mòn bị tắc nghẽn nhanh chóng.
Giải pháp:Sử dụng đá mài có độ nhám thô hơn và cấu trúc mở khi làm việc trên vật liệu mềm hơn. Điều này giúp ngăn chặn tải nhanh và cho phép loại bỏ phoi hiệu quả.
Ô nhiễm vật liệu:
Gây ra:Các chất gây ô nhiễm có trong vật liệu phôi, chẳng hạn như dầu, mỡ hoặc cặn chất làm mát, có thể góp phần gây ra tải trọng.
Giải pháp:Đảm bảo vệ sinh đúng cách phôi trước khi mài để loại bỏ chất bẩn. Sử dụng chất lỏng cắt hoặc chất làm mát thích hợp để giảm thiểu tải.
Sử dụng chất làm mát không đúng cách:
Gây ra:Việc sử dụng chất làm mát không đủ hoặc không đúng cách có thể dẫn đến việc bôi trơn và làm mát không đủ, gây ra tải.
Giải pháp:Tối ưu hóa lưu lượng và nồng độ chất làm mát. Đảm bảo chất làm mát tiếp cận hiệu quả vùng nghiền để bôi trơn và làm mát quy trình, ngăn ngừa tải.
Độ sắc nét của bánh xe không đủ:
Gây ra:Đá mài cùn hoặc mòn sẽ dễ bị tải hơn vì chúng mất đi hiệu quả cắt.
Giải pháp:Thường xuyên mài và làm sắc đá mài để duy trì độ sắc của đá mài. Sử dụng máy mài đá mài để làm lộ các hạt mài mới và tăng cường hoạt động cắt.
Tốc độ bánh xe thấp:
Gây ra:Vận hành đá mài ở tốc độ thấp có thể không tạo đủ lực ly tâm để đẩy phoi ra, dẫn đến hiện tượng tải.
Giải pháp:Đảm bảo máy mài hoạt động ở tốc độ khuyến nghị cho sự kết hợp cụ thể của bánh xe và phôi. Tốc độ cao hơn có thể giúp loại bỏ phoi tốt hơn.
Áp suất quá mức:
Gây ra:Áp dụng quá nhiều lực trong quá trình mài có thể đẩy vật liệu vào bánh xe, gây ra tải trọng.
Giải pháp:Sử dụng áp lực mài vừa phải và đồng đều. Điều chỉnh tốc độ cấp liệu để bánh xe có thể cắt hiệu quả mà không có áp lực quá mức dẫn đến tải.
Thông số kỹ thuật bánh xe sai:
Gây ra:Sử dụng đá mài có thông số kỹ thuật không phù hợp với vật liệu cần mài có thể gây ra tải trọng.
Giải pháp:Chọn bánh mài có loại mài mòn, kích thước hạt và độ liên kết phù hợp với ứng dụng cụ thể. Việc kết hợp bánh mài với vật liệu giúp ngăn ngừa tải.
Vệ sinh chất làm mát không đủ:
Gây ra:Chất làm mát bị ô nhiễm hoặc cũ có thể gây ra vấn đề về tải.
Giải pháp:Thường xuyên vệ sinh và thay thế chất làm mát để ngăn ngừa sự tích tụ chất gây ô nhiễm. Chất làm mát mới và sạch sẽ tăng cường khả năng bôi trơn và làm mát, giảm khả năng tải.
Kỹ thuật mặc quần áo không đúng cách:
Gây ra:Việc định vị đá mài không đúng cách có thể dẫn đến hiện tượng không đồng đều và tải trọng.
Giải pháp:Chỉnh bánh xe đúng cách bằng dụng cụ chỉnh bánh xe phù hợp. Đảm bảo rằng hình dạng bánh xe đồng đều và không có bất thường để tránh tải.
Giải quyết hiệu quả các vấn đề về tải bao gồm sự kết hợp giữa lựa chọn bánh xe phù hợp, thiết lập máy và các biện pháp bảo dưỡng. Người vận hành nên tuân theo các quy trình được khuyến nghị, sử dụng các thông số mài phù hợp và thực hiện việc mài bánh xe thường xuyên để giảm thiểu tải và tối ưu hóa hiệu suất mài.
Việc lựa chọn đĩa mài phù hợp là rất quan trọng để đạt được kết quả tối ưu trong nhiều ứng dụng gia công kim loại và chế tạo. Việc lựa chọn phụ thuộc vào các yếu tố như vật liệu đang gia công, độ hoàn thiện mong muốn và loại máy mài đang sử dụng.
Lựa chọn đĩa mài phù hợp
Khả năng tương thích của vật liệu:
Kim loại đen (Thép, Sắt):Sử dụng đĩa mài được thiết kế riêng cho kim loại đen. Các đĩa này thường chứa chất mài mòn phù hợp với độ cứng của thép và ít bị tải hơn.
Kim loại màu (Nhôm, Đồng thau):Chọn đĩa có chất mài mòn phù hợp với kim loại mềm hơn để tránh tắc nghẽn. Đĩa nhôm oxit hoặc silicon carbide là những lựa chọn phổ biến.
Vật liệu mài mòn:
Nhôm oxit:Thích hợp cho mục đích mài chung trên kim loại đen. Bền và đa năng.
Zirconia Alumina:Mang lại hiệu quả cắt cao hơn và tuổi thọ cao hơn, phù hợp để mài mạnh trên kim loại đen và kim loại màu.
Cacbua silic:Thích hợp để mài kim loại màu và đá. Sắc hơn nhưng kém bền hơn nhôm oxit.
Kích thước hạt:
Hạt thô (24-36):Loại bỏ vật liệu nhanh chóng và nghiền mạnh.
Độ nhám trung bình (40-60):Cân bằng giữa việc loại bỏ vật liệu và hoàn thiện bề mặt.
Hạt mịn (80-120):Mang lại bề mặt mịn, thích hợp cho việc chuẩn bị bề mặt và mài nhẹ.
Loại bánh xe:
Loại 27 (Trung tâm bị đè nén):Đĩa mài tiêu chuẩn có bề mặt phẳng, lý tưởng cho việc mài bề mặt và mài cạnh.
Loại 29 (Hình nón):Thiết kế góc cạnh để loại bỏ vật liệu mạnh mẽ và trộn bề mặt tốt hơn.
Loại 1 (Thẳng):Được sử dụng cho các ứng dụng cắt. Nó cung cấp một cấu hình mỏng để cắt chính xác.
Ứng dụng:
Mài:Đĩa mài tiêu chuẩn để loại bỏ vật liệu và định hình.
Cắt:Sử dụng đĩa cắt để cắt kim loại, tạo ra cạnh thẳng và sạch.
Đĩa Flap:Kết hợp mài và hoàn thiện trong một. Thích hợp để pha trộn và làm mịn bề mặt.
Khả năng tương thích với máy xay:
Đảm bảo đĩa mài tương thích với loại và tốc độ của máy mài đang sử dụng. Kiểm tra khuyến nghị của nhà sản xuất về RPM (Vòng quay mỗi phút) tối đa của đĩa.
Tính cụ thể của nhiệm vụ:
Loại bỏ vật nặng:Chọn loại đá mài thô và đĩa loại 27 hoặc loại 29 để loại bỏ vật liệu hiệu quả.
Hoàn thiện bề mặt:Chọn loại có độ nhám từ trung bình đến mịn với đĩa mài để có bề mặt nhẵn mịn hơn.
Những cân nhắc về an toàn:
Thực hiện các hướng dẫn về an toàn, bao gồm việc đeo thiết bị bảo vệ cá nhân (PPE) phù hợp như kính an toàn và găng tay.
Chọn đĩa được gia cố để tăng thêm độ bền và an toàn.
Thương hiệu và chất lượng:
Chọn đĩa từ các thương hiệu uy tín, nổi tiếng về chất lượng và độ đồng nhất. Đĩa chất lượng cao mang lại hiệu suất và độ bền tốt hơn.
Cân nhắc về chi phí:
Cân bằng chi phí ban đầu với tuổi thọ dự kiến và hiệu suất của đĩa mài. Đĩa chất lượng cao có thể có chi phí ban đầu cao hơn nhưng có thể mang lại giá trị tốt hơn theo thời gian.
Bằng cách xem xét các yếu tố này, người vận hành có thể chọn đúng đĩa mài cho ứng dụng cụ thể của mình, đảm bảo hiệu quả, an toàn và kết quả tối ưu.
Phần kết luận
Tóm lại, việc lựa chọn đĩa mài phù hợp là một khía cạnh quan trọng để đạt được kết quả gia công kim loại và chế tạo thành công. Sự lựa chọn phụ thuộc vào nhiều yếu tố như vật liệu đang gia công, độ hoàn thiện mong muốn và loại máy mài đang sử dụng. Bằng cách xem xét khả năng tương thích của vật liệu, loại mài mòn, kích thước hạt, loại bánh xe, ứng dụng, khả năng tương thích của máy mài, tính đặc thù của nhiệm vụ, độ an toàn, chất lượng thương hiệu và chi phí, người vận hành có thể đưa ra quyết định sáng suốt để nâng cao hiệu quả và độ an toàn trong quy trình mài của họ.
Điều cần thiết là phải tuân thủ các hướng dẫn về an toàn, đeo thiết bị bảo vệ cá nhân phù hợp và làm theo khuyến nghị của nhà sản xuất về khả năng tương thích của máy mài và đĩa. Cho dù là để loại bỏ vật liệu nặng, hoàn thiện bề mặt hay ứng dụng cắt, đĩa mài phù hợp có thể ảnh hưởng đáng kể đến chất lượng và hiệu quả của công việc.
Ngoài ra, việc kiểm tra định kỳ tình trạng hao mòn, giải quyết các vấn đề như quá nhiệt và rung động, cũng như hiểu rõ các vấn đề về tải sẽ góp phần kéo dài tuổi thọ của đĩa mài và đảm bảo hiệu suất ổn định.
Tóm lại, một phương pháp tiếp cận có hệ thống và hiểu biết sâu sắc để lựa chọn, sử dụng và bảo dưỡng đĩa mài là chìa khóa để đạt được kết quả tối ưu, nâng cao năng suất và đảm bảo môi trường làm việc an toàn.
Thời gian đăng: 12-01-2024